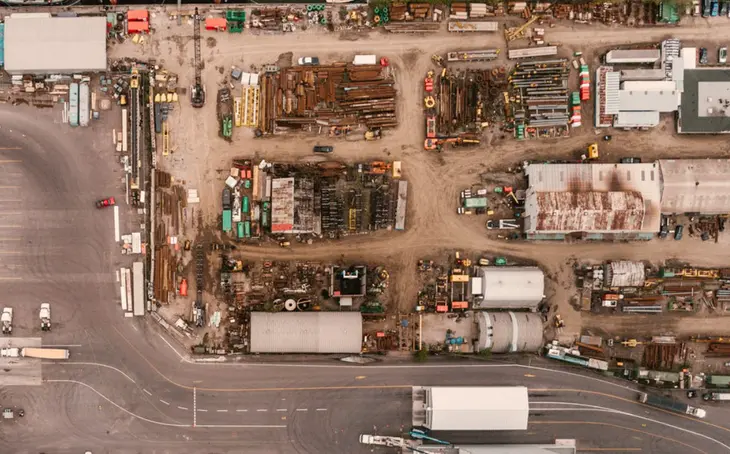
Step 11: Implementing Production Processes
- Admin
In Step 11 of our guide to building your factory, we focus on implementing production processes, a pivotal phase that transforms your plans into tangible operations. This step involves installing and configuring equipment, testing production workflows, and fine-tuning processes to ensure efficiency and quality. Let's delve into why implementing production processes is crucial and how to approach it effectively.
Why Implementing Production Processes is Crucial:
Implementing production processes marks the transition from the planning phase to actual manufacturing operations. It is the stage where raw materials are transformed into finished products, and the success of your factory hinges on smooth execution. Effective implementation ensures that your factory operates efficiently, meets production targets, and delivers high-quality products to customers, ultimately driving profitability and competitiveness.
Key Components of Implementing Production Processes:
Equipment Installation: Install and set up manufacturing equipment according to design specifications and safety standards. Ensure that equipment is calibrated, connected, and functioning correctly before proceeding to production.
Testing and Validation: Conduct comprehensive testing of production processes to identify and resolve any issues or inefficiencies. Test equipment functionality, process workflows, and quality control measures to ensure they meet performance requirements.
Training and Skill Development: Provide training to production staff on equipment operation, safety procedures, and quality standards. Invest in ongoing skill development and continuous improvement initiatives to enhance workforce capabilities and productivity.
Optimizing Workflows: Analyze production workflows and identify opportunities for optimization and streamlining. Implement lean manufacturing principles, such as reducing waste, improving cycle times, and maximizing resource utilization, to enhance efficiency and productivity.
Quality Control and Assurance: Establish robust quality control measures to monitor product quality throughout the production process. Implement inspection protocols, testing procedures, and corrective actions to maintain consistent quality standards and prevent defects.
Strategies for Effective Implementation:
Phased Approach: Break down the implementation process into manageable phases or milestones to facilitate systematic progress and minimize disruption. Prioritize critical tasks and allocate resources accordingly to ensure smooth execution.
Cross-Functional Collaboration: Foster collaboration and communication between different departments and stakeholders involved in production implementation, including engineering, operations, quality assurance, and maintenance. Encourage teamwork and knowledge-sharing to address challenges and drive continuous improvement.
Continuous Monitoring and Adjustment: Monitor production processes closely during the initial implementation phase and beyond. Track key performance indicators (KPIs), gather feedback from frontline workers, and address any issues or bottlenecks promptly to maintain momentum and course-correct as needed.
Flexibility and Adaptability: Remain flexible and adaptable in response to unforeseen challenges or changes in market conditions. Anticipate potential disruptions and have contingency plans in place to mitigate risks and ensure business continuity.
Conclusion:
Implementing production processes is a critical milestone in the journey of building your factory. By installing equipment, testing workflows, and optimizing processes effectively, you can lay the foundation for efficient and high-quality manufacturing operations. Stay tuned for the next step in our guide to building your factory!
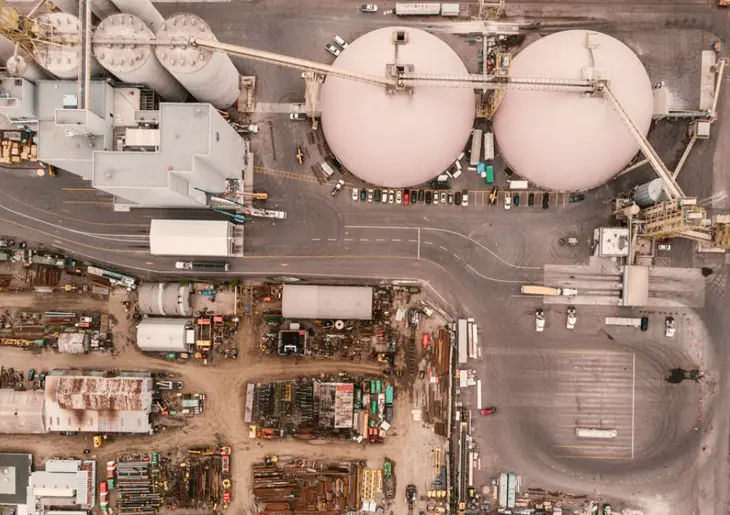